As the wave of AMI and smart meter deployments begins to crest, many utilities are poised to turn their attention to what is widely anticipated to be the next major focus area for Smart Grid projects – Distribution Automation. In particular, the automated isolation and restoration of distribution feeder faults is one application that can have significant impact on improving system reliability and quality of service, while laying the foundation for additional feeder optimization. After all, how valuable will the bevy of new intelligent power meters and home area networks be if the distribution system is unable to reliably and efficiently deliver quality power to the consumer? The good news is that there are now more options available when it comes to the implementation of automated feeder restoration systems – particularly solutions that use a model-driven scheme. This article will discuss some of the basics of this technology, and highlight some recent advancements that will give utilities more flexibility in its application.
Smart Grid App… Before Its Time
“Self-healing” feeder networks are typically implemented using two approaches - scripted (rules-based) and modeldriven. The model-driven approach is often referred to by various acronyms, including FDIR (Fault Detection, Isolation and Restoration) and FLISR (Fault Location, Isolation and Service Restoration) This automated detection of feeder faults and reconfiguration to restore power to un-faulted sections is a Distribution Automation application that has now been around for many years. It can be argued that FDIR (the acronym we’ll use for this discussion) is a true Smart Grid application that was somewhat ahead of its time.
While this level of unattended feeder reconfiguration was somewhat slow to gain traction in North America, some international utilities have embraced the technology early on with positive results. As early as 1998, the Taiwan Power Company implemented what is generally considered the first fully automated DA/DMS system, using FDIR on approximately 800 distribution feeders to cut typical service restoration times on un-faulted sections from 60 minutes down to only 20 seconds.
Increased Focus on Reliability & Performance
Since the late 1990s, utility performance regulations (reward/ penalty structures) and increasing penetration of distributed energy resources and microgrids have increased pressure on utilities to respond efficiently to distribution faults and quickly restore power to as many customers as possible. The automated fault handling performed by FDIR provides many benefits to the utility and the customer that are well chronicled. These benefits include:
- Shorter outage durations
- Fewer sustained outages
- Improved performance indices
- Enhanced operational efficiencies
- Improved service quality
Feeder Automation Approaches Diverge; Goals Remain
Across North America, utilities have deployed many different solutions to achieve the fault isolation and restoration functionality. Some use distributed rules-based applications that rely on pre-determined topology and fault scenarios; others have more robust control-center configurations with a three-phase unbalanced load-flow model to enable additional feeder optimization functionality.
Ultimately, all restoration technologies share the same core objectives; that is, to:
- Accurately detect and locate feeder faults
- Isolate the faulted portion(s) of the feeder
- Restore power as quickly as possible (upstream and/or downstream of the faulted section).
FDIR is traditionally deployed as an advanced system-level application running on the distribution management system (DMS) in the control center. In recent years, some other methods of applying feeder restoration technology have entered the marketplace. There are still essentially two basic types of self-healing feeder architectures in use – distributed and centralized.
The distributed approach moves the automation intelligence out into the devices located along the feeders using scripted logic and peer-to-peer communication, while the centralized approach utilizes a control-center based algorithm and requires direct communication between the control center and the devices in the field.
The Distributed Approach
With the distributed approach, controller devices at the switch/ breaker location contain the automation logic needed to restore a selected portion of the network. These devices communicate among themselves in a peer-to-peer fashion to determine where the fault has occurred and to determine the appropriate switching actions necessary for restoration.
Since the intelligence needed for restoration is localized and distributed among the controllers, this approach uses preprogrammed, or scripted, solutions based on a known baseline topology for that section of the network. Since no real-time network model is utilized, the system can have difficulty handling multiple faults and must usually be deactivated if the network is in an abnormal state (e.g., if any temporary switching has been performed). If the system is expanded, vendor services are usually needed to reprogram the restoration logic to include the additional feeders and devices.
The controllers in a distributed system are generally vendorspecific and often must interface with another automated control or feeder RTU at the switch, or may double as the switch control themselves. In either case, basic controller requirements for FDIR include the ability to detect feeder fault currents, detect voltage loss upstream of the switch, and store historical load data at the switch, which is then used to make downstream restoration switching decisions.
Some of the pros and cons of the decentralized approach are:
- Pros: Faster performance; quicker deployment; suitable for small “islands” of automation
- Cons: Requires more field maintenance/programming; specialized equipment needed; lack of real-time network model limits flexibility; unnecessary switch operations performed by opening up all switches before isolating the fault
The Centralized Approach
The centralized architecture is a model-driven solution and typically involves running FDIR as a subsystem of the distribution management system at the control center. Since the restoration intelligence is resident within the DMS, no specialized controllers are required at the substation or switch. This allows the utility to leverage automated controls that may already be in place. If these switch or recloser controls are capable of fault current detection, then no additional hardware may be required at all. If the fault detection capability is not provided by the switch control, then there are a number of low-cost RTU options available that can provide the needed telemetry.
Unlike the pre-programmed logic used in the distributed scheme, centralized FDIR utilizes a real-time load flow model of the network, meaning restoration actions can take place even if abnormal network conditions exist. It handles multiplefault scenarios effectively. It makes possible more complex switching scenarios and load-transfer decisions such as a secondary load transfer to create additional capacity on the alternate feeder.
Using the model and the telemetered data, the FDIR application develops a switching sequence to restore as many de–energized feeder sections as possible using a minimum number of switching actions within the allowed overload and voltage drop limits of the impacted feeders and power sources. Another advantage of the centralized scheme is that FDIR can be configured to operate in a semi-automatic or automatic mode. In semi-automatic mode, the application creates the necessary restoration switching plan, but does not perform the actions until approved by the operator.
In 2003 Cobb EMC – located near Atlanta, Georgia – implemented a sensor-based location system using a private radio network to help speed up the location of faults on its more than 7,000 miles of line. Cobb, one of the largest member-owned cooperatives in the US, took that a step further in 2008 when centralized FDIR was added to the system to take full advantage of the more than 650 remotely controlled switches on its system.
Some of the pros and cons of the centralized approach include:
- Pros: model-based solution can effectively handle abnormal network conditions; can increase ROI through other feeder optimization applications (e.g., Integrated Volt/VAR Control); all data is available at the control center; no specialized field equipment required; no re-programming required for expansion
- Cons: requires controller communication directly with control center; larger implementations can be costlier; requires an accurate network load model before implementation
Today: A “Best of Both” Evolution?
While the two general schemes discussed here may remain the firstorder choice for implementing feeder automation, there are evolutions of each of these basic architectures that can provide utilities with a combination of the advantages provided by both. A “semi-distributed” system is a model-driven scheme in which the FDIR algorithm is hosted at the substation level instead of at the control center. In this configuration, an intelligent substation controller serves as the field “host” for FDIR, utilizing a local network connectivity model updated with real-time topology for the area of automation. All feeder devices that are part of the automation scheme communicate back to the substation level only, and specialized field hardware is not required.
The FDIR controller at the substation can also act as a data concentrator, communicating back to a primary SCADA or DMS system for enhanced system visualization at the control center level. Expansion to multiple substations and feeders within the automation “island” is accomplished through the appropriate updates to the network model. The model can be updated offline when network updates or additions are made, and then downloaded to the controller remotely or loaded locally at the substation.
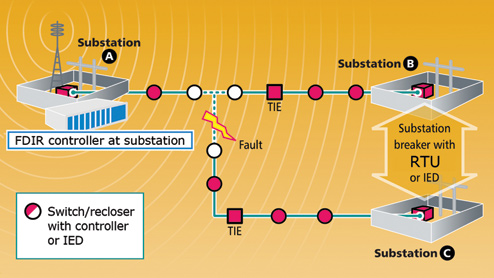
In a semi-distributed approach, an FDIR model is resident at one substation within the “island.”
As an alternative to the traditional centralized architecture, utilities can also choose a separate centralized system that provides the benefits of the model-based approach to FDIR without the up-front cost and resources typically required to develop the network model. New ways to configure systems can simplify the process of creating this network model by using pre-defined network templates to create automation “islands.”
The system provides the user a matrix of templates for differing numbers of substations, feeders and switches, allowing the utility to select the one that matches a particular island. A simple menu-based tool then helps define the specifics for each device in the chosen template (i.e., switch control, communications parameters, etc.).
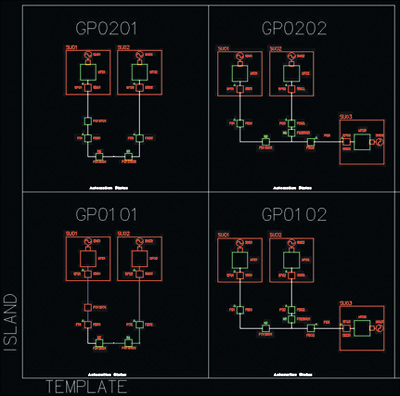
A new centralized system can use pre-defined “island”
templates to build a network model for FDIR quickly.
Using this approach, an automation island can be configured and operational in less time than it takes to program and implement a rules-based peer-to-peer system, at a comparable cost. This standalone type of centralized system links easily to a SCADA or DMS. It can expand to include other model-driven applications such as Loss Minimization and IVVC – providing further justification to the utility for the investment in an automation system.
This year, a major IOU in the south will pilot a system using this approach. Developed by Efacec ACS, the system will automate three independent templates with up to 15 devices in each – including switches, reclosers and breakers. Communicating with field devices using DNP/IP with IDEN modems, the system will provide FDIR functionality without operator intervention, using existing IED controllers already on the utility network.
Additional features will include:
- Substation dead-bus detection
- Interface to SCADA system
- Protection Function status monitoring
- ‘Return-to-Normal’ function
- Restoration status indicators
- Manual start for restoration after loss of voltage on transmission
FDIR: A Key Driver of Smart Grid Future Tech
The wave of architecture options and technology choices has not yet crested. It continues to evolve as utilities today pursue the most effective feeder restoration solution to support their distribution automation systems. DA looks to be a Smart Grid trend that will see increased utility investment in the coming years. In an era in which demonstrable efficiency and customer satisfaction are increasingly important, FDIR is poised to play a vital role as a technology that delivers clear improvements in both.
The two traditional approaches to self-healing feeders have distinct pros and cons that must be carefully weighed when making planning and investment decisions. Yet with the newest innovations in model-driven FDIR system architectures, utilities are no longer limited to choosing between the two.
New combined approaches are bringing important advantages over either approach alone, depending on the unique aspects of each deployment. If each approach has formerly forced utilities to choose which wave to ride, the new technology is like two waves converging, offering users a powerful combination of tools to reach their goals. In fact, the future of FDIR may be an empowered utility in which users are likely to find that a mix of these architectures and systems allow them to define a hybrid approach that provides them with the best performance and value.
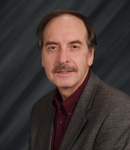
Chief Technology Officer
Efacec Advanced
Control Systems
Gary Ockwell holds a BSEE Degree from University of Saskatchewan (Saskatoon, Saskatchewan, Canada). From 1973 to 1985, he worked for SaskPower Corporation in Canada, serving as the project manager for the Gas & Electric System Control Project and Manager of the Control Department. From 1985 to 1995, Ockwell worked for Harris Controls Division as a Product Manager. He joined Advanced Control Systems (now Efacec ACS) in 1995 where he now serves as chief technology officer. Ockwell is also a longstanding member of the IEEE Power & Energy Society.