Electric utilities are facing increasing pressure to provide superior quality and reliable service to their customers while also seeking higher efficiency in their work forces and processes. As a result, key trends in electric utilities best practices are improving facilities and infrastructure visibility, as well as implementing preventive maintenance programs. Improving operational visibility helps teams identify and address issues before they become service, safety, or compliance issues. As part of that operational visibility, many electric utilities are working to improve inspection and reporting processes for lines, substations, poles, and vegetation management. Immediate access to this data on conditions can improve preventive maintenance and streamline operations.
The Electric Vehicles ARE Coming!
A recent Tennessee Valley Authority (TVA) report demonstrated how timely preventive maintenance can save millions of dollars in repairs and replacements. Over a single 6-month time period, TVA calculated savings of $4.3 million by performing preventive maintenance in a sample of 106 substations. After assembling the right team for inspections and surveys, TVA concludes that, “thorough documentation is the next key ingredient.”
Many of these workflows have resisted data collection with laptops and PDAs, due to the highly mobile nature of the work, and challenge of complex equipment, training, and support. In many cases, data collected to track these processes is still written by hand on printed forms, maps, and CAD designs, which slows the process.
The Challenge: Getting Data off Paper for Timely Analysis and Reporting
All that documentation means a lot of paperwork process; many highly mobile teams collect inspection data directly on paper forms, CAD designs, and maps. Pen and paper survives for a variety of familiar reasons:
- There is no training required – anyone can fill out forms or markup plans and maps.
- Paper can be used in any environment – indoors, outdoors, rain, or direct sunlight.
- Large format paper maps and CAD prints enable a wide field of view – important for understanding and marking up extensive maps or complex plans.
Writing notes on paper is easy, of course. The challenge is getting data off paper in a timely way, so that important information can be quickly tracked and shared. In many cases, data collected on paper creates an administrative burden.
Completed forms, marked-up maps, and CAD designs usually need to be scanned or sent back to central operations. Depending on the workflow, there is often manual data entry required back at the central office, where data is entered into the central IT system for analysis and sharing. In the case of inspection forms, data can be tracked in custom systems or even simply in Microsoft Office. In the case of maps, data on poles and lines is often stored in a GIS system. In the case of substations, marked up data often needs to be entered into computerized drawing systems as the master record of facilities and their as-built conditions.
New Options for Utilities: Digital Pen Technology
Many utilities are exploring the use of digital pen and paper technology and software to help streamline data collection and reporting for line, pole, and substation inspections, and vegetation management. Digital pens enable mobile teams to collect data on paper as they always have, while also instantly scanning and digitizing the data, which gets stored on the pen. Such software enables utilities to print their own maps, CAD drawings, and forms and then use digital pens to automatically collect data directly into various files and file formats from CAD systems. After data is collected, it can be shared with central offices either immediately through a cell phone connection or physically, when the pen is returned to the office.
Burbank Water and Power
Burbank Water and Power, for example, is using digital pen technology to automate data collection to keep their substation plans current and manage preventative maintenance. The utility – located just outside Los Angeles – serves 45,000 households and 6,000 businesses in Burbank, California, with power and water through an extensive network of poles, lines, substations, and water infrastructure. BWP substations undergo frequent inspections, repairs, and preventive maintenance in order to provide customers with high service levels and uptime. The frequent changes result in as-built drawings being out-of-date and as much as years of paper-based updates backlogged for CAD operators. BWP is currently working with Capturx Software for digital pens to instantly capture substation as-built mark-ups to improve infrastructure visibility, while reducing data collection and entry costs and risks from missing documentation.
Keeping Substation Plans Current w/ Frequent Maintenance Changes
Like many utilities, BWP has skilled maintenance and service teams, which inspect critical infrastructure, perform preventive maintenance, and quickly respond to issues to keep service levels high. As teams plan and perform maintenance on substations, for example, they work with as-built drawings which reflect the original plans along with the cumulative changes. Armed with the current drawings, service teams can bring the right parts and tools and avoid surprises.
The challenge is that the plans are often out of date. With ongoing maintenance, parts and configurations frequently change. Changes are noted on the paper drawings in real time, but it can take as months, or even years, for those changes to be reflected in the master as-built drawings. Marked up paper plans can be misplaced, left on site, or left in trucks. When the markups do make it back to the office, the CAD operator adds them to the stack of marked-up drawings awaiting updates.
Such delays can be costly in time and money as well as in other ways. Out-of-date substation plans make it difficult to plan preventive maintenance and react proactively to issues. Out-of-date plans can also result in surprises onsite when teams respond to issues with equipment and staff that don’t match the actual substation conditions.
Mobile Computers: Too Cumbersome for Substation Inspections & Service
To get the as-built markups back to the CAD operators faster and reduce the risk of missing documents, the team had explored using mobile computers. Laptops and tablets did not end up being a viable alternative for a variety of reasons.
For one thing, the teams are highly mobile and work in demanding environments – industrial, outdoors, or bright sunlight. In addition to requiring extra cost for equipment, training, and support, mobile computers typically only offer a keyhole view on CAD plans. This makes it difficult to work with and mark up bigger and more complex CAD design drawings. The teams also weren’t necessarily trained on CAD systems, which can be complex, so the easiest process is the current process; that is, simply redlining large paper prints with a pen.
With the new software, field workers can simply print CAD drawings of the substation plans, which are published directly out of the CAD system (in this case, AutoCAD). The designs are printed on ordinary paper and markups to specific drawings can be tracked easily with digital pens. Redlines are scanned as they are written with the digital pens, which record the ink strokes and automatically associate them with the correct files published from AutoCAD. When field teams return to the office, they simply connect the digital pens to their PCs over a USB port. The redline markups are then automatically integrated into the correct design files.
Faster Substation Inspection Reporting and Plan Updates
Substation inspection and service teams can now digitize their markups on site as they write them on paper. The data can be instantly sent to the back office using the pen’s built-in Bluetooth with cell phones or stored on the pen during the day, or even a week, for uploading into the original files through a standard PC and USB connection. With faster access to digital data, CAD operators can get files in digital formats immediately, resulting in faster updates.
Reduced Risk with Real-Time Data Access and Better Visibility
With better and faster access to data, teams can more quickly spot issues, better plan preventive maintenance, and avoid risks from unidentified issues. Should the paper get lost or destroyed, the pen records all information. Likewise, if the pen is lost or damaged before data is downloaded, the inspector still has the original paper forms.
Works the Way They Do
BWP was able to automate the substation inspection and as-built updating process without any complex or expensive computers, training, support, or distractions. The teams in the field simply continue the easy and reliable process of writing and redlining paper substation plans. Engineers can focus on their core tasks – inspecting, reporting, identifying, and addressing issues – without the costs, risks and delays of the paper trail.
Utilities such as Burbank Water and Power are looking to digital pen technology because it frees up time and improves access to data. Typically inspectors and technicians do the data entry, which takes time away from inspecting and analysis and simply collecting data. Software that enables data from digital pens to be automatically integrated into native Microsoft Office, ESRI ArcGIS, and PDF files can save a great deal of data entry time. Teams can focus on their core tasks – inspecting, reporting, identifying, and addressing issues.
Since data is instantly digitized and can be immediately sent to central offices from the field, teams can also speed up access to data collected in the field with digital pens. The speed can improve dealing with simple one-off issues that are noted in the field for immediate attention. On a larger scale, it can also result in more efficient maintenance scheduling. For teams managing a range of facilities, immediate visibility to facilities issues enables more efficient deployment of service personnel to address the issues.
Faster data access and eliminating data entry can reduce a range of risks from delayed issue reporting to data entry errors, leading to unaddressed problems, as described above. In many cases, utility teams face a great deal of risk simply from missing paper. Data on paper frequently never makes it back to central offices – having been left at facilities, the truck, or lost in transition from the truck to the scanner or data entry clerk. Missing paper can range from a simple inconvenience to a large liability in the case of key regulatory inspections, adherence to safety procedures, or interactions with stakeholders and private and public property owners.
Conclusion
Many electric utilities are working with digital pen and paper technology to help streamline a range of field processes that have resisted automation with PCs in the past. In addition to the examples above for inspections and facilities tracking, many teams are also automating other paper form processes, including safety reports and time sheets. The common thread is that teams working with paper but needing digital access to either scanned paper, structured data tables, or immediate access to sketches and signatures. For many utilities like BWP, pen computing might be just the answer they’ve been looking for!
About the Author
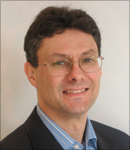
Pietro Parravicini started his career in the Logistics and Transportation sector in Zurich, Switzerland in 1984. He subsequently held financial and operational management positions with Siemens, Alusuisse and ProData Treuhand, exposing him to a variety of other industries and international businesses. In 1995, he joined Siemens-Nixdorf AG as Director of Finance and Operations and became a member of the Management Group, overseeing IT solution business units within Public Sector, Telecom and Banking & Insurance.
After relocating to the U.S. in 1997, Parravicini was appointed Vice President and CFO at Siemens Nixdorf Retail & Banking Systems Inc. and Wincor Nixdorf Inc., and served as member of the board. He gained experience in corporate management, acquisitions, spin-offs and re-organizations. Parravicini holds a degree in business administration from the Swiss Business School, Zurich (Switzerland) and earned subsequent degrees in corporate financial management. He joined Anoto Inc. in April 2001.