Just a few years ago, many utilities faced overwhelming growth pressures. Construction crews couldn’t hook up new customers fast enough. Engineering drafters had trouble keeping up with demands for designs to support network expansions. And geographic information systems (GIS) analysts had huge backlogs of as-built information. Utilities like Arizona Public Service (APS), looked for ways to accomplish more with limited resources. Technology helped by allowing utilities to move away from paper to drive processes and communication improvements.
As the economy sputtered, growth slowed. But as the old saying goes, the more things change, the more they stay the same. Utilities still need to do more with fewer resources – and here again, technology plays a key role. To succeed, the computer-based processes utilities need to accomplish their work quickly and cost-effectively must be made more efficient, automated, and connected.
Focusing on the way it designs its underground distribution network, APS embraced new model-based design technology to accelerate the process. Virtually every task in the design workflow is now faster and more accurate. In fact, in the early stages of using this technology, the small group of designers who use it are able to complete many jobs more than 50 percent faster. The technology couldn’t have come at a better time: as APS rolls it out to their designers, they are getting ready to support a return to growth—and help enable innovative design approaches as customers look to use more sustainable generation sources.
Overwhelming Growth
Originally incorporated in 1886, APS is now the largest subsidiary of the Pinnacle West Capital Corporation, and it delivers electricity to 1.2 million customers over a 35,000-square-mile service area. The company experienced significant growth in the 1990s, with annual growth rates as high as 8 percent. Attracted by Arizona’s sunny climate and booming economy, people streamed into APS’s service area. Real estate developers were constructing new subdivisions at a breakneck pace, and each subdivision needed to be served by new underground distribution systems.
The APS Energy Delivery Business Unit was overwhelmed with underground facility design projects. Each project took weeks to complete because at every stage in the design, APS drafters were slowed by manual processes. Take the preliminary design stage: Drafters produced a design for the developer that included information for permitting and trenching for electrical conduits. (The developers, and not APS, dug the conduit trenches.) The preliminary designs were relatively similar to each other, but drafters had to draw each element into its appropriate place in their CAD software. The entire process took about two weeks – and as much as four weeks or longer for large subdivisions.
After approval, drafters completed the final designs and produced construction documentation, including the bills of materials (BOM). Although the preliminary design provided some information to help with the final, many aspects were redrawn. This ’rework’ slowed this stage in the process as well, but having to complete engineering calculations in a separate application took an even larger toll. Not only time-consuming, the disconnected calculation process introduced the potential for inconsistencies into the workflow. To save time, drafters often slightly over-engineered designs and over-ordered materials, such as wires and pipes. Under-provisioning can lead to extremely costly delays in the field, but over-specifying can be costly too, especially when it is a practice commonly exercised.
After construction, GIS specialists entered the new network information into the GIS, which is the source of spatial network data for the outage management system. Unfortunately, this process required that the specialist redraft the as-built designs into the GIS, and as-built backlogs of several months were common.
Although customer service agents were able to provide accurate information to affected customers, due to wall maps, and older outage prediction technology, this lag time sometimes made it difficult for field crews to locate the specific device(s) affected.
Connecting and Automating
Business leaders at APS decided to tackle inefficiencies in the underground facility design process by implementing a new design solution. APS identified five must-have requirements for the solution:
- Increase efficiency and productivity across the design team
- Capture and transfer institutional knowledge to offset the impact of impending retirements
- Reduce design cycle times dramatically
- Automate and standardize business processes, including pricing models, engineering calculations, and design techniques
- Improve data integrity
Through the years, frustration with slow design cycles inspired similar decisions – as well as efforts to find the right technology to accelerate the process. APS evaluated several technologies and found each had too many drawbacks. Some network design solutions executed designs and calculations too slowly, and APS did not see any advantage in shifting from manual processes to automated processes that were not much faster. Other solutions APS explored required too much setup and configuration on the front end, or too much retraining for APS’s 400 CAD users.
Automation Saves Time
APS opted to implement the new utility design solution by targeting incremental phases to minimize risk and hoped to demonstrate early success. The first phase focused on configuring the solution to automate repetitive tasks and establish business rules. APS began by selecting a new subdivision slated to receive single-phase power as a pilot project. The team automated compatible unit and material specifications, such as those for transformers, streetlights, and junction boxes. At the same time, they automated repetitive tasks, including replacing streetlight blocks, dimensioning, and service arrow placement. They also configured the solution to generate wire and streetlight summaries that conformed to APS standards.
To ensure quality, APS validated and fine-tuned many of the solution’s preconfigured aspects. For instance, the team ran engineering calculations for cable pulls, transformer sizing, and voltage verification within the solution. They then recalculated each one manually and found the calculations were accurate and in line with APS standards.
Throughout the phase one implementation, APS rigorously tracked time savings enabled by the new solution. The results were impressive, especially for repetitive tasks. The table below summarizes a few of the more notable time savings per task in minutes and seconds:
Procedure | Before | After | Time Saved |
Cable pull program | 1:50 | 0:07 | 1:43 |
Service arrows | 6:54 | 0:57 | 5:57 |
Dimensioning | 2:38 | 0:11 | 2:27 |
Streetlight blocks | 1:40 | 0:22 | 1:18 |
Overall, APS determined that drafters were able to execute automated tasks up to five times faster, allowing them to complete designs in less time. Just as important, automation freed them to devote more of their time and expertise to enhancing design quality.
Moving to Phase Two
After completing phase one, the implementation team shared the results of the project more widely throughout the Energy Delivery Business Unit. The recorded time savings helped generate enthusiasm for moving the full underground distribution design process to the solution. More ambitious, the second phase of the project encompassed the end-to-end process for designing underground distribution for a three-phase feeder, commercial development, and subdivision.
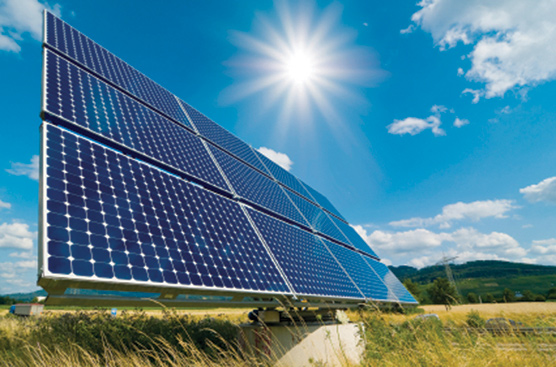
Gila Bend Solar Plant
The team began by importing the vicinity map for the projects from the GIS. After validating the accuracy of the imported data, they began the preliminary designs for delivery to the developers. To drive time savings in this stage, the team automated trench detail labels and configured the solution to support the full range of engineering calculations required for underground three-phase power distribution. Still tracking time savings, the team was able to cut completion time for the preliminary designs by about a third.
Full integration of the solution with the IBM Maximo Asset Management system is a key future goal. APS wants the systems to work together to seamlessly generate work order package forms that included everything from the circuit diagrams and cable tag list to the pole installation report and the equipment details. The team is confident that the standardization enforced by the new system will help streamline the integration and support more accurate BOMs. More significantly, from a cost perspective, the automated engineering calculations will help prevent over-ordering of materials.
Upon completion of the three projects, the APS team assessed the effort’s success. The team was able to complete the commercial project 47 percent faster and the subdivision project 48 percent faster. The time savings were even more impressive on the feeder design, with APS completing that project in 64 percent less time.
The Rooftop Revolution
While saving time on routine designs is a compelling benefit, moving the overhead design process to the new solution could help support an even more exciting – and revolutionary – program. APS recently undertook one of the most innovative alternative energy pilot projects in the United States.
The idea could turn entire neighborhoods into clean energy power producers. The program works like this: Homeowners allow APS to put solar panels on their rooftops. APS buys, owns, and maintains the panels. The power goes into the system, and APS sells power to the homeowner at a reduced rate. The project is being piloted with a small group of homeowners in Flagstaff, Arizona.
The program could help transform the way renewable power is generated and sold in Arizona. Once the design project moves to overhead, APS will be able to help deliver relevant designs with appropriate compatible units and modified engineering calculations based on solar technology quickly and efficiently. So, in a sense, APS’s improved design process will extend from underground – to the sun.
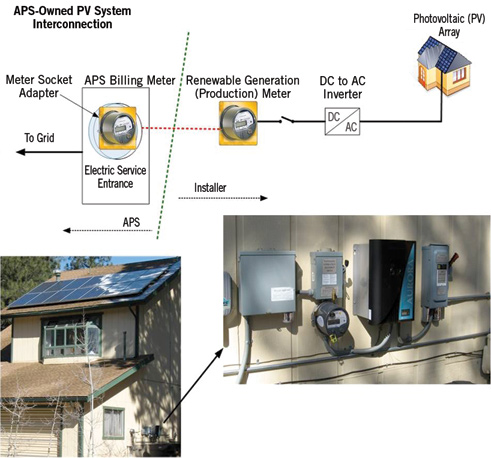
APS-Owned PV System Interconnection
Looking Ahead to Overhead
APS finished phase two in October 2009, and rolled out the new solution to support underground distribution projects. The APS design team was now primed and ready to complete more designs faster than ever before. But growth had ground to a near halt. Developers were simply not breaking ground on new subdivisions that demanded underground distribution networks.
Of course, APS is a large utility, so there is always a demand for design work. As backlogs disappeared, maintenance projects pushed to the backburner during Arizona’s recent growth boom took on new urgency. The underground design team turned their attention to projects affecting the existing distribution system and was able to execute them more quickly. And as they reviewed the old distribution designs, they noted significant inconsistencies and deviations from some current APS standards. The new solution made it easy to clean up old designs, increasing the accuracy of the information used to drive projects and manage the distribution system.
Since APS has experienced staff cuts and limited capital funding, the new underground Autodesk Utility Design solution has not been rolled out as quickly or to as wide an audience as originally envisioned. Consequently there is still a significant amount of ‘anchoring’ to be done. However, the team is still planning to develop the overhead design processes within the solution.
By driving distribution design tasks with a single solution, APS will be able to extend the time savings of process automation to all design tasks. It also will embed a fuller range of institutional insights, and corporate ‘tribal knowledge’ into the solution – an important benefit with many of APS’ experienced designers nearing retirement age. But most important, it will ready APS for the return to the consistent growth that has long been the norm for Arizona.
About the Author
Brett Hauf is an Information Systems Manager at Arizona Public Service, a Pinnacle West company. Prior to APS, Brett worked for other utilities in the area. He has 28 years experience in Cartography/Mapping, CAD and GIS, including 23 years in the electric transmission and distribution business. In his present role at APS, he partners with Business Line Managers to ensure alignment between information systems and the technology needs of key APS initiatives.