According to the Department of Energy, today’s electricity system is 99.97 percent reliable. But when the flow of electricity to customers is cut off, the Department of Energy says this loss of power costs Americans at least $150 billion each year. Sometimes the sheer size of the grid can blind us to the fact that behind all the technology are utility professionals. These engineers, line personnel and many others keep the grid and its 300,000 miles of transmission lines operating. In the end, the Smart Grid will be far brighter if we have more visibility into the work of the people running and repairing the grid.
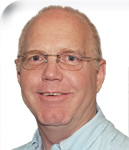
Mark Hungate
Field Maintenance Manager
Salt River Project
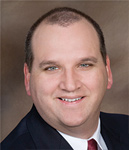
Mitch McLeod
President & CEO
ARCOS, Inc.
By now most all of us have seen the GEICO caveman commercials. The premise is that cavemen live among us today, and they are anything but the Neanderthals that we commonly associate with that term. Rather, they are urbane and highly intelligent. It’s funny stuff and gets GEICO’s message across, albeit in a lighthearted manner.
It may come as a surprise then to learn that many distribution and emergency operations managers see ‘cavemen’ working alongside them every day all across the utility industry. Like their TV counterparts, these utility cavemen are very smart and quite capable. Yet the way they’re being asked to go about carrying out some very important tasks is anything but intelligent – and their plight certainly isn’t funny.
Let’s say a pole goes down after normal business hours in our territory. We call a supervisor who has to search through a paper list and start dialing available crewmembers from his kitchen table in the middle of the night. We jokingly refer to that process as ‘caveman callout’ because smart people are being forced to use outdated methods to get the job done.
Today, the utility industry can’t always easily and precisely identify problems with the grid. Indeed, in many cases, outage notification is still largely a manual process. That is, they rely on customers to “call in” the outage and roll trucks to the affected area(s) to track down the root cause and any ancillary problems – often a slow and painstaking process. In the end, these antiquated processes affect the grid’s IQ and hence, its ability to respond intelligently.
For example, intelligent utility professionals with a long list of action items that they should be addressing during an outage are, instead, forced to hunt for available crew members like cavemen foraging for food. This one-at-a-time search for members of a repair crew unnecessarily lengthens the time of any outage. The process also delays restoration work, which frustrates customers, and costs a lot of money for utilities. More on that last point in a moment…
Manual callout is a process that’s buried and in many ways under the surface of evolving Smart Grid technologies. In some instances, utility executives have even come to accept that manual callout and resource management is just the price of doing business – but it’s not. The growing complexity of the Smart Grid includes things like optical current sensors that can tell utilities instantly that a fault has occurred as well as where it is located. Other smart technologies can even help us fix some distribution problems, for example, by remotely flipping substation switches.
Also on the horizon is the development of advance visualization technology for the grid. These tools, it is hoped, will be able to report the grid’s condition to utilities on both a national and street level. And someday, information about blackouts and the quality of the power being generated will all be at a utility company’s fingertips as well – some truly amazing stuff. As an industry we’re clearly heading in the right direction, but identifying a problem with the grid is not the same as fixing it.
The Importance of Restoration
Customers are less tolerant of power outages than ever before. So, for our industry, restoration time has become increasingly important. Actually implementing innovative technologies across the utility industry has not been high on many companies’ to-do lists. The utility industry is usually very conservative; however, we need to spend money on not only developing new technologies, but also implementing them to address our top concerns: Reliability and Restoration Time. Yet some operation centers still rely on paper-based wall maps and have just begun using computer programs for opening and closing circuits remotely.
Because of all the regulations and scrutiny, many utility companies are reluctant to spend the money on technology – even technology we really need – because of how much work it is politically to get systems approved. Automating callout needs to be on everyone’s list of priorities.
If the Smart Grid is to help customers open a window into what’s causing an outage and how long it will take to resolve, then utilities should focus on compressing restoration time like never before. Some utilities are taking bold steps in that direction. Xcel Energy’s SmartGridCity project – a real-world lab where the utility explores an array of smart-grid tools in Boulder, Colorado – helps Xcel decide how to bring field-tested smart-grid technology into its business operations to net more efficiency. Customers, armed with new insight, will demand it.
– Mark Hungate (SRP)
Restoration time, especially after normal business hours, often hinges on how quickly a company can contact its available line personnel, assemble a crew and bring the team to the scene of an outage. For many utility companies across the United States, that process is still a manual one. One utility company in the Northeast, which for many years relied on an outmoded crew callout process for after-hours emergencies, states that its manual process took, on average, almost 80 minutes to assemble and dispatch a crew.
A Cascade of Challenges
The grid may be getting smarter, but when a storm knocks a power line down causing an outage, it is up to line personnel to put things back together. Even one incident like this creates a cascade of challenges for the utility personnel who manage emergencies, let alone a large storm causing lots of outages. Prolonged outages are also a financial drain for utility companies, investors and the consumers of electricity. Here’s why…
Without a smart system for managing resources and crew callout, a utility facing an after-hours outage must call a supervisor at home, sometimes in the middle of the night. The supervisor grabs a cell phone and a thumb-worn file of available line personnel. He or she begins calling each name to try and get a crew assembled. When you are relying on a cell phone and a pad of paper to put together a crew late at night, it can often take one or two hours to reach available workers who are willing and able to accept the assignment. Often, compounding the callout process is a complex set of union rules that dictate which linemen can be called and in what order. If a sleep-deprived supervisor happens to run afoul of those rules, the union can file a grievance.
For a utility relying on a manual callout and resource management process, grievances like these can tally well over $100,000 per year. Even when the process runs smoothly, a utility still has to pay wait time (i.e., overtime) for each member of the crew who has accepted a callout, until the final member of a four-person crew agrees to work the situation.
In fact, the average utility company spends nearly $500,000 annually in what is commonly called ‘paid wait’ time.
Along with grievances and paid wait time comes lost meter revenue. The Smart Grid’s growing list of technologies, such as electronic actuation of switches, is wonderful. But when systems fail and a call for help goes out, the time lost between the alert and the repair spells lost revenue.
To show the cumulative effect of antiquated callout, consider the following real-life example from a utility with 1,904,531 customers. While still relying on “caveman callout,” this utility’s SAIFI number and CAIDI minutes were pegged at 0.74 and 185, respectively. SAIDI minutes for the utility were 137, which converted to SAIDI hours of 2.28, slightly higher than the median value of 1.5 SAIDI hours for North American utilities, as measured by the Institute of Electrical and Electronics Engineers (IEEE). Customer meter revenue per hour stood at $0.12.
After crunching the numbers (i.e., Customers x SAIDI Hours x Meter Revenue per Hour), the utility learned that lost meter revenue across all their customers due to slow callout totaled $521,411 for the year. But after automating its callout and resource management processes, the utility saw a 20 percent improvement in restoration time and $104,282 in annual recovered meter revenue.
In the case of grievances, these are dollars that utility executives can avoid completely if they choose to make callouts smarter. Managers could also drastically cut paid wait time and shave time off lost meter revenue by managing their human resources with technology. Moving from a manual process to an automated one takes an investment to be sure. But implementing callout technologies delivers reporting tools to managers who can use this information to validate crew availability. These automated tools call hundreds or thousands of line personnel in a few seconds, while factoring into each call the complex union rules and labor agreements for overtime and rest.
Automated Callout: Pinpointing an Overlooked Area for Innovation
The utility industry is investing in technologies to give managers visibility into the grid and data on grid performance. As part of this innovation, utilities of all sizes are at least hearing about – if not implementing – projects for improving hardware, software and work methods. Utilities such as Kansas City Power & Light, Southern Company and Dominion Virginia Power are among the ones looking at efficiencies to get resources where they are needed, faster.
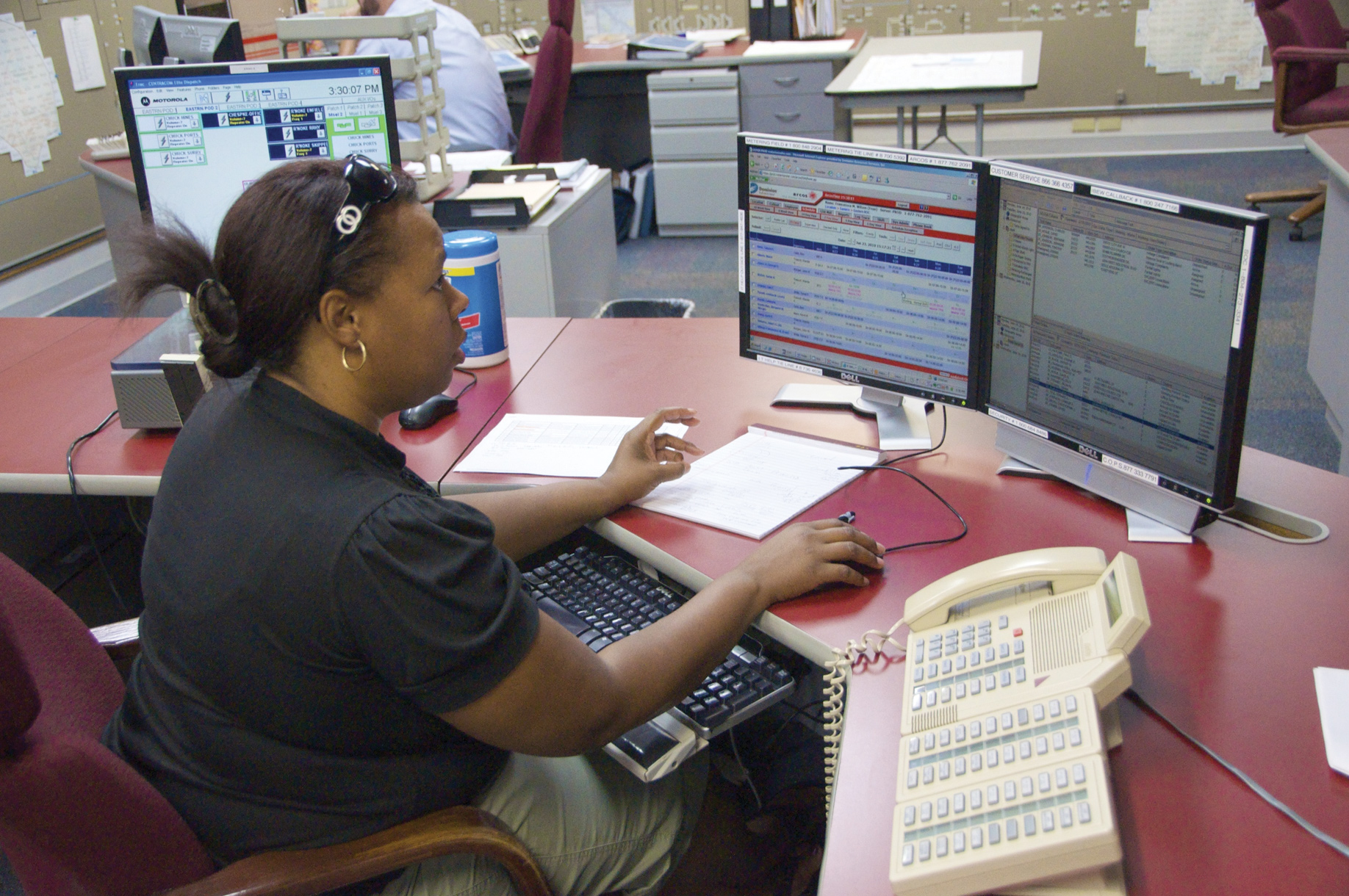
High-ranking utility executives everywhere can benefit by applying this thinking to their workforces. Utility industry executives often focus on how to make the work happening in the field more efficient. There is a desire to zero in on the line work, but trimming the elapsed time between contacting crews about trouble and getting them into their trucks to make repairs is an area often overlooked.
According to a utility executive from the Northeastern United States: “Automating callout and resource management is an innovative solution to a process that’s always going to be needed. To complement the Smart Grid, crew callout and resource management should be underpinned by technology that serves up performance metrics based on bargaining agreements. It should monitor the time it takes to respond to emergency conditions. And it should manage crew rotations and hours worked.”
If we could shave even ten percent off restoration time with better callout and resource management technology, just think of what it would mean for the bottom line! Sure, it’s fun to watch the GEICO cavemen, but nobody really wants to become one when there’s serious work to be done.
About the Authors
Mark Hungate is Field Maintenance Manager for Salt River Project, America’s third-largest public power utility. Mark is responsible for line crew maintenance on SRP’s electric system. Mark has nearly three decades of experience in the utility industry since beginning his career as a lineman.
Mitch McLeod is CEO of ARCOS, Inc. Since 1997, Mitch and his team have provided the utility industry with automated crew callout and resource management systems. Mitch is an expert in software development and voice applications. Before founding ARCOS, he worked for the U.S. Department of Defense and AT&T Bell Laboratories. Mitch holds a master’s degree in software engineering from Johns Hopkins University.